The food industry is undergoing a significant digital transformation, particularly in terms of food safety processes. Digitizing these processes is becoming essential for auditing and monitoring purposes.
Initiatives like the FDA’s “New Era of Smarter Food Safety” and the GFSI’s “Race to the Top” underscore the increasing importance of digital track and trace systems. Full traceability is becoming mandatory in various global markets, with countries like China and Australia leading in stringent food safety requirements.
The need for digital supply chain management is also being driven by large food retailers imposing stricter traceability demands on manufacturers.
In response to these demands, food manufacturers must prioritize data collection as a foundational step towards improving food safety through enhanced traceability. This digitization effort can also streamline other digital initiatives within the company, such as optimizing production efficiency.
The journey towards digital food safety involves several key steps, beginning with a thorough audit of existing data collection and food safety processes. Many companies will find that they already have much of the necessary data and processes in place due to existing food safety certifications.
However, the current state of data collection is often fragmented, with a mix of digital and manual methods being used. The challenge lies in unifying this diverse array of hardware and software into a cohesive digital food safety program.
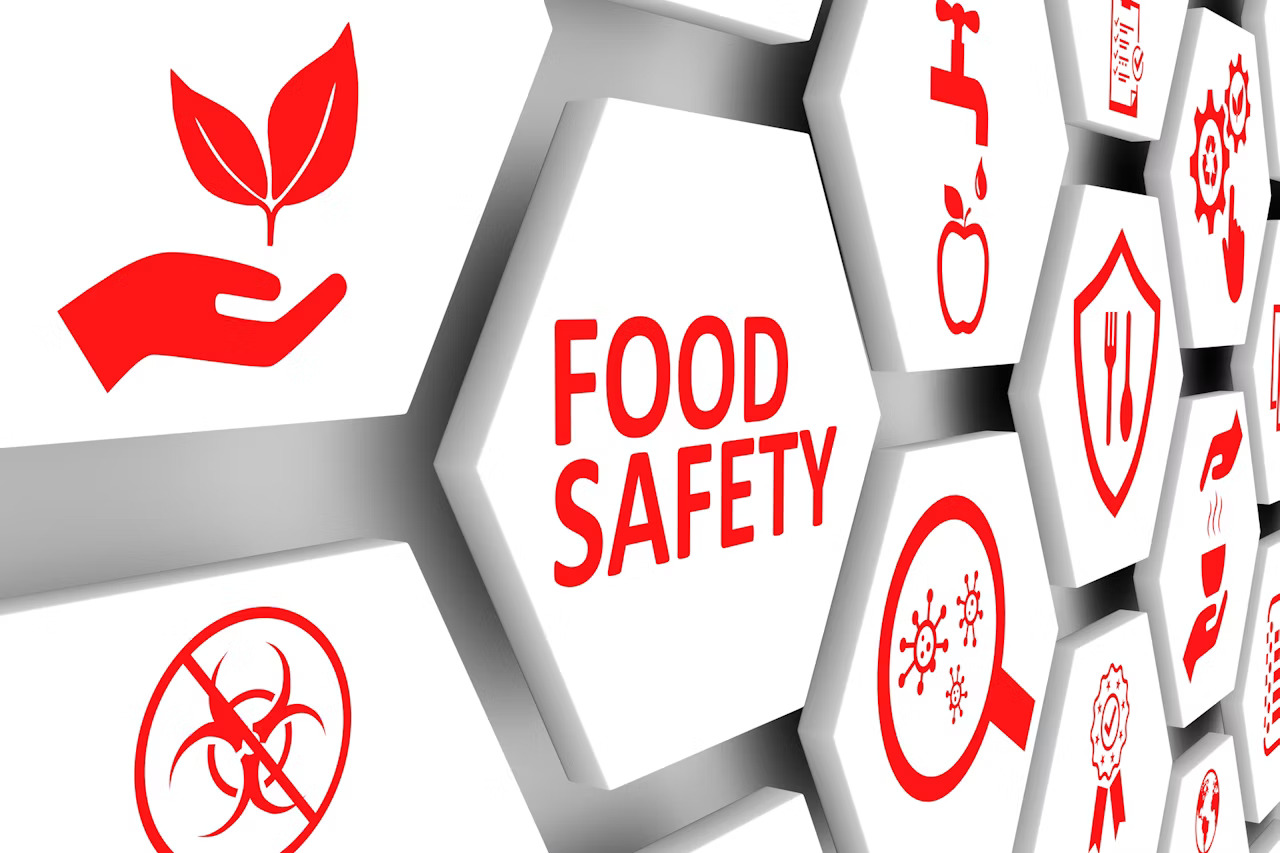
Technological complexity is compounded by the age and variety of systems in use, many of which were not designed for modern IoT or Industry 4.0 standards. Global standards and communication protocols, such as OPC U/A, GS1 Digital Link, and EPCIS 2.0, can help reduce this complexity and facilitate a smoother transition.
A strategic approach is crucial in developing a digitalization strategy. Companies need to define their specific applications and long-term digitization goals, whether they aim for basic regulatory compliance, production process optimization, or a comprehensive digital transformation aligned with IoT and Industry 4.0.
Central to this strategy is data exchange, which enables quick identification of specific batches’ locations. Engaging with suppliers and system manufacturers early on can reveal existing capabilities that may not require complete system overhauls but rather simple upgrades or new software options.
Building and securing expertise is another critical step. Companies must identify all internal and external stakeholders involved in digital food safety and assess their existing knowledge and gaps.
This includes formulating data-sharing guidelines and determining who needs access to specific data throughout the product life cycle. Engaging with stakeholders in the value chain is essential for creating a comprehensive overview of expertise and addressing any knowledge gaps.
Institutionalizing change management is vital as the digitization of food safety impacts various departments and entails significant organizational changes. Proactive management of this cultural shift is necessary to ensure employee understanding and acceptance of increased data transparency.
Leadership and commitment are required to drive the changes forward, with a multi-stakeholder group addressing common benefits and concerns. Senior executive sponsorship and continuous communication with management teams are essential to keep the transformation process on track. A roadmap with manageable goals can help in achieving quick and tangible benefits from digitization.
By strategically adopting digital food safety and planning the digital transformation of the supply chain, food manufacturers can transition smoothly and cost-effectively. Many companies may find they are already well-positioned to begin this transformation.
Despite the technological complexity, the tools and protocols available today make the process relatively straightforward and user-friendly, ensuring minimal business disruption and substantial long-term benefits.